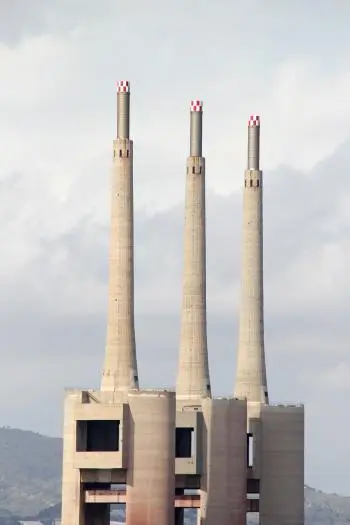
A thermal power plant is a power station in which heat energy is converted to electric power. In most of the world, thermal power plant turbines are steam-driven. Water is heated, turns into steam, and spins a turbine that drives an electrical generator. After it passes through the turbine, the steam is condensed in a condenser and recycled to where it is heated; this is known as a Rankine cycle.
The most significant variation in the design of thermal power stations is due to the different heat sources: fossil fuel, nuclear energy, or renewable energy, such as solar energy or biomass.
A thermal power plant is an electric plant that converts thermal energy into electrical energy. The difference between one type of plant and another is how the heat is obtained.
How does a steam power plant work?
A steam power plant works using a thermodynamic cycle describing the process by which energy is extracted from fuel and converted into electricity.
In a typical thermal power plant, fuel (such as coal or natural gas) is burned in a boiler to produce heat. The heat is then used to generate high-pressure steam in a steam turbine, which drives an electrical generator. Next, the generated electricity is supplied to the grid for distribution to consumers. Finally, the resulting steam passes through a heat recovery boiler to restart the power cycle.
A steam power plant cycle's thermal power generation efficiency depends on the temperature difference between the working fluid in the boiler and the cooling water. The higher the temperature difference, the higher the power supply efficiency.
The power generation of the cycle of these generation plants is the same regardless of how heat is obtained.
Components of a Steam Power Plant
The main parts of a steam power plant are
-
Fuel source: it is the source of power, and the most popular fuels are coal and natural gas. Nevertheless, some stations use a non-conventional source of energy, such as solar power.
-
Boiler: In the boiler, the fuel is burned to obtain thermal energy and generate steam.
-
Turbine: the stream drives the steam turbine to get mechanical energy.
-
Generator: it is responsible for converting kinetic energy into electrical energy.
-
Condenser: it cools down the steam to get a liquid fluid again and restarts de Steam cycle.
What are combined cycle power plants?
A combined cycle power plant is a type of thermal power plant that uses a gas turbine in conjunction with a steam turbine to generate electricity. The two turbines are connected to a typical generator.
The advantage of a combined cycle power plant over other types of thermal power plants is that it is more efficient. For example, the efficiency of a combined cycle power plant can be as high as 60%, while the efficiency of other types of thermal power plants is typically only around 30%.
This increased efficiency is due to the waste heat from the gas turbine can be used to generate steam, which the turbine can then use to create additional electricity.
The fuel for this type of plant is natural gas, diesel, and even coal if prepared in a particular way.
The main characteristic of the gas cycle is that the fluid has no phase change. Therefore, the process is the following: gas compression, gas heating, and finally, gas expansion in a gas turbine. In this case, the turbine is connected to an electric generator to produce electricity.
The gas that comes out of the gas turbine is still at a very high temperature, so it is used to generate steam and activate a conventional steam cycle in parallel.
The Rankine Cycle
The Rankine cycle is the most common steam power plant cycle. It's a closed-loop system that uses water to create steam and drives a turbine to produce electricity. Then, finally, the steam is cooled and condensed back into water, pumped back into the boiler to start the cycle over again.
The Rankine cycle is named after William John Macquorn Rankine, a Scottish engineer who developed it in 1859.
The ideal Rankine cycle is shown in the p-v and T-s diagrams below. It consists of four processes:
-
1-2: Boiling water to steam at constant pressure (isobaric process).
-
2-3: Expanding steam through a turbine at constant entropy (isentropic process).
-
3-4: Condensing steam at constant pressure (isobaric process).
-
4-1: Pumping water back into the boiler at constant entropy (isentropic process).
In an actual Rankine cycle, there are efficiency losses due to irreversibilities (frictional losses in the turbine and heat exchanger, for example). These can be minimized by using superheated steam and reheating it before it enters the turbine. Reheat also increases the power output of the cycle without increasing the steam consumption.
Steam power plants running on solar energy
Solar thermal power plants use the sun's rays to generate steam. As a regular steam power station, the steam is used to turn a turbine, which powers an electrical generator.
Solar thermal power plants can be either "concentrating" or "non-concentrating." In a concentrating plant, mirrors focus the sun's rays onto a small area, which heats a working fluid running through it.
In a non-concentrating plant, the mirrors reflect sunlight onto a large receiver filled with fluid. The heat from the sun warms this fluid, which then turns the turbine. Solar thermal power plants are usually built in dry, sunny areas.
The solar energy concentration at this point generates very high temperatures used to create steam.
From here on, the operation is the same as in any conventional thermal power plant.
Advantages of a Thermal Power Plant
There are many advantages of a thermal power plant.
-
They are relatively inexpensive to build and operate.
-
They can be built quickly, which is essential in areas where there is a need for new power plants but not enough time to wait for a nuclear plant to be constructed.
-
Natural gas combined cycle plants are much more efficient (reaching 60%) than conventional thermal power plants.
Disadvantages of a Thermal Power Plant
Thermal power plants are not without their disadvantages, however.
-
One major disadvantage is that they are a leading cause of air pollution due to the emissions from the smokestacks. These emissions can include sulfur dioxide, nitrogen oxides, and particulate matter.
-
Thermal power plants are also a leading source of greenhouse gas emissions, primarily in the form of carbon dioxide. Currently, thermoelectric plants are obliged to control their emissions. This obligation is particularly relevant for large power plants where there is an important section to reduce pollutants.
-
They can also cause water pollution. For example, the cooling towers associated with thermal power plants use large quantities of water, which can be a source of water pollution if it is not treated correctly.
-
Coal-based power plants are often located in areas with a high demand for electricity but a limited water supply. This can put a strain on local water resources.