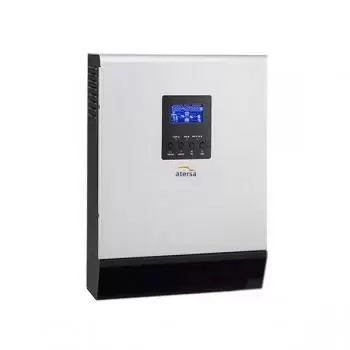
A power inverter is an electronic device. The function of the inverter is to change a direct current input voltage to a symmetrical alternating current output voltage, with the magnitude and frequency desired by the user.
In the beginning, photovoltaic installations used electricity for consumption at the same voltage and in the same form as they received it from solar panels and batteries. That is, it worked with a continuous current of 12, 24 or 48 volts.
This feature made a big difference with users who had an electrical distribution network or 220 volt alternating current generator sets. For this reason, electric inverters were introduced.
What is a power inverter for?
Inverters are used in a wide variety of applications, from small computer power supplies to industrial applications.
Below we list some examples in which an electrical inverter is used:
-
In a photovoltaic installation they are used to convert the direct current supplied by the solar panels into alternating current.
-
In uninterruptible power supplies of an electrical installation, the inverter converts the voltage supplied by the battery into alternating current.
-
In the transmission of electrical energy, the inverter converts the energy into direct current transferred in some power lines to feed the alternating current grid.
-
The realization of a switching power supply, for transformation into direct current, with considerable advantages in terms of efficiency, size and weight
-
In the aerospace sector, they are used to provide aircraft avionics with a highly stable alternating current even if supplied by batteries (in the event of a power failure)
-
Speed variation in electric motors.
How does an inverter work?
A simple inverter consists of an oscillator that controls a transistor, which is used to interrupt the incoming current and generate a rectangular wave.
Sine wave inverters have a transformer that softens their shape making it look a little more like a sine wave. A good technique to achieve this is to use the PWM technique, making the main sinusoidal component much larger than the higher harmonics.
The square waveform generated by these devices has the problem of being rich in higher harmonics, while the sine wave of the power grid is devoid of them.
Advantages
-
It is the type of current that is used throughout the world and, therefore, gives a point of normality.
-
It makes it easier to purchase appliances to be able to access the ones that are most efficient.
-
It allows maintaining stable voltage and waveform values, despite the variability of the batteries' state of charge.
-
Working with higher voltages (220V is 18 times 12V) allows working with a lower current intensity in accordance with Ohm's law. In this way, thinner electrical conductors can be used and losses due to the Joule effect are minimized.
Disadvantages
-
The installation consists of one more element, the converter. Therefore, the reliability of the system decreases.
-
The converter has electrical losses to compensate by generating more electricity to the modules (5%).
-
In small installations, the converter can represent a significant part of the budget; For example, for an installation with about 100 Wp of module power, a 250 W converter can represent 20% of the total cost.
Main features
Main characteristics that define a converter
-
Input voltage (Vcc): this value must be equal to that of the battery (12, 24, 48 V).
-
Output voltage (Vac): this value must be normalized (230 Vac).
-
Output/input voltage stability: Variations of up to 10% are supported for square wave converters and 5% for sine wave converters.
-
Wave type: Currently, inverters must present a standardized alternating current type format with a pure sine wave.
-
Overload capacity (peak power) and thermal protection: very useful in installations with motors, since at start-up the power necessary for nominal operation can be doubled, although only for a few seconds.
-
The energy efficiency or performance of the converter is the relationship between the energy that the converter provides for alternating current consumption and the energy that this input converter needs (from the battery).
-
Automatic start and standby state: allows the power parts of the same converter to be disconnected in the absence of consumption. They then reconnect when they detect an energy demand above a previously set threshold.
-
Protection against polarity reversal and short circuits: basic options, given the possibilities of error or malfunction of the consumer circuits, which are high during the life of the converter.
-
Low harmonic distortion: parameter related to the quality of the generated wave. Harmonics are normally eliminated by filters, although this entails losses. The frequency variation of the output voltage will be less than 3% of the nominal.
-
Possibility of being combined in parallel: it will allow a possible growth of the installation and power consumption.
-
Good behavior with temperature variation: operating range between -5ºC and 40ºC.
Power inverters for solar cells
The inverters of photovoltaic systems for entry to the electrical grid are designed specifically for this purpose. Its function is to transform electrical energy in the form of direct current produced by solar cells into alternating current to be able to supply it to the electrical grid.
Below are some types of inverters used in solar energy systems:
String Inverters
These inverters are the most common in residential and commercial systems.
They convert the energy of several solar panels connected in series (a string) into alternating current. They are suitable for medium-sized systems and offer a good balance between cost and performance.
Microinverters
Each solar panel has its own microinverter connected directly to it. This allows for greater control and efficiency, as each panel operates independently. They are especially useful in systems where shading or obstruction may affect one or more panels.
Central inverters
These inverters are used in large-scale systems such as commercial and utility-scale solar plants. They convert energy from multiple solar panels into a single central unit. They are efficient and suitable for high performance systems.
Hybrid Inverters
Hybrid inverters not only convert solar power from DC to AC, but can also work in energy storage systems such as batteries. This allows the use of stored solar energy at night or on cloudy days.
Grid-Tie Inverters
These inverters are used in solar systems that are connected to the electrical grid. They convert solar energy into AC and allow the injection of electricity into the public grid. Some models also allow the energy generated and consumed to be measured.
Off-Grid Inverters
These inverters are used in stand-alone solar systems that are not connected to the electrical grid. They convert DC solar energy to AC to power devices and systems in remote or off-grid areas.