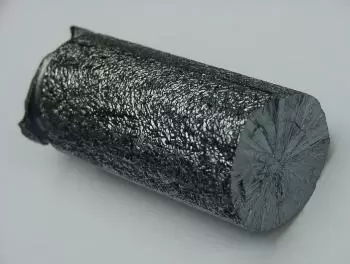
Polycrystalline silicon is a material composed of multiple misaligned silicon crystals. It serves as an intermediate between amorphous silicon, which lacks long-range order, and monocrystalline silicon, which has a continuous crystal structure.
Polycrystalline silicon has an impurity level of 1 part per billion or lower, making it suitable for high-tech applications.
Properties of Polycrystalline Silicon Cells
Polycrystalline silicon cells exhibit distinct characteristics that influence their efficiency, durability, and overall performance:
- Efficiency: Typically ranges between 12% and 21%, lower than monocrystalline cells but sufficient for most applications.
- Manufacturing Process: Made by melting silicon scraps, cooling them to form a crystalline structure, and cutting them into wafers.
- Appearance: Recognizable by their blueish hue and grainy, multi-crystal structure, which differentiates them from the uniform black appearance of monocrystalline cells.
- Cost-Effectiveness: Less expensive to produce than monocrystalline silicon cells due to simpler manufacturing techniques.
- Temperature Sensitivity: Slightly more sensitive to temperature variations, which can lead to minor efficiency losses under high heat.
- Durability: Comparable lifespan to monocrystalline panels, often exceeding 25 years, making them a reliable choice for solar energy applications.
Applications of Polycrystalline Silicon
1. Photovoltaic Energy
Polycrystalline silicon plays a crucial role in solar energy production, particularly in the manufacturing of photovoltaic (PV) cells.
There are two main types of photovoltaic panels:
- Monocrystalline panels – Made from single-crystal silicon, offering higher efficiency.
- Polycrystalline panels – Made from polycrystalline silicon, which is more cost-effective but slightly less efficient.
The choice between monocrystalline and polycrystalline panels depends on performance requirements and budget considerations.
2. Electronics
Polycrystalline silicon exhibits moderate metallic properties, allowing it to replace aluminum in semiconductor components. It is widely used in integrated circuits due to its mechanical strength and stability.
In integrated capacitors, polycrystalline silicon forms the conductive plates, while silicon oxide serves as the dielectric. Compared to high-purity silicon used in advanced electronics, polycrystalline silicon can be produced using simpler and more cost-effective techniques.
Polycrystalline Photovoltaic Panels
Polycrystalline solar cells have an efficiency range of 12% to 21%. They are often produced by recycling discarded electronic components—known as "silicon scraps"—which are remelted to create a uniform crystalline structure.
The manufacturing process involves melting silicon residues in a crucible, cooling them to promote vertical crystallization, and forming a silicon block (typically 150–200 kg). This block is then sliced into ingots and further cut into thin wafers similar to those used in monocrystalline solar cells. The wafers are cleaned with a soda solution and doped with phosphorus to form PN junctions, essential for solar energy conversion.
How is Polycrystalline Silicon Produced?
Most polycrystalline silicon is manufactured as gray cylindrical rods with a rough dendritic surface. These rods are broken into fragments and packed in polyethylene bags for distribution.
The production process typically involves:
- Seeding – A mono- or polycrystalline silicon seed is introduced to initiate crystal growth.
- Crystallization – Compact crystallites, resembling short needles, develop from the seed.
- Dendritic Growth – Under high sedimentation rates, dendritic structures may form, affecting the final material quality.
The purity of the seed significantly impacts the electrical resistivity and overall quality of the polycrystalline silicon rod.
Polycrystalline Silicon and Conversion Efficiency
Polycrystalline silicon generally has lower purity and efficiency than monocrystalline silicon. However, its production in fluidized bed reactors offers advantages, such as greater surface deposition and better utilization of raw materials.
Despite these benefits, granular silicon produced this way often contains amorphous material and fine particles from the reactor lining. As a result, it is primarily used for manufacturing solar-grade glass and polycrystalline solar panels, where ultra-high purity is less critical.